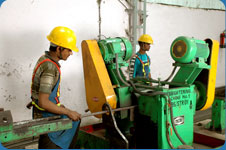
STRAIGHTENING OPERATION
After confirming the raw material round bars ranging from Ø12mm to Ø32mm from lab, first operation is straightening the bars to ensure uniform straightness to facilitate in peeling and grinding operation. These bars are visually checked by rolling them on plane surface.
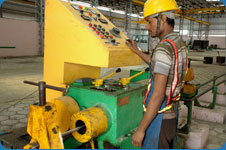
PEELING OPERATION
Extra material and surface defect (rolling defect) are removed by this process.
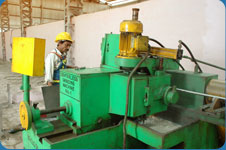
CENTRELESS GRINDING OPERATION
Centreless Grinding is done to make the bars smooth finish and maintain the finished bar’s diameter.
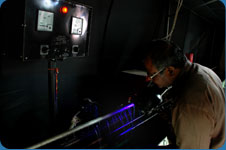
MAGNAFLUX TESTING
By this test cracks and seam are detected on the bars. OK bars are sent for next operation. And cracked bars are to be rejected.
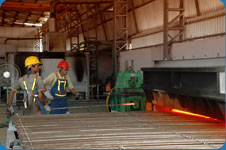
TAPER ROLLING OPERATION
Ends of the bars are heated in the furnace ; ends are taper forged to give 75% firm bearing. These bars are taper rolled on the machine to maintain taper length, tip thickness, squeezing length. Stamping on the rods is also done during this operation for identify grade, manufacturer, date, month and drawing no.
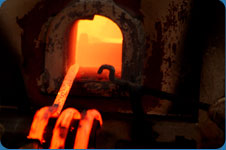
COILING AND HEAT TREATMENT
Taper rolled bars are heat treated in the furnace at a temperature of about 900 oC. These rods are coiled on the CNC based coiling machine and quenched immediately in quenching oil. These hardened springs are tempered to remove the stress that have been induced during the process. The tempered springs come out from the tempering furnace through conveyor belts and are cooled in air.
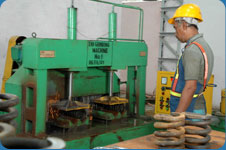
END GRINDING OPERATION
Both faces of spring are ground up to 75% of mean diameter for proper seating in the assembly.
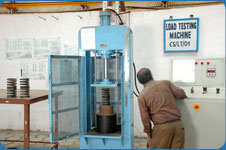
LOAD TESTING
Spring compressed with specified working load and loaded height of individual spring is measured. Springs are grouped accordingly.
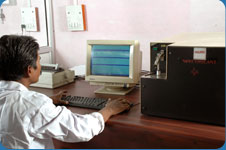
CHEMICAL TESTING
With the help of spectrometer machine, chemical analysis of the sample cut from the round bar and spring is done.
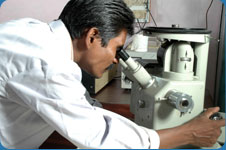
METALLURGICAL TESTING
Metallurgical microscope coupled with image analysis software is used for analyzing inclusion rating, depth of decarburization, grain size, macro examination of the cut samples from round bar and the spring.
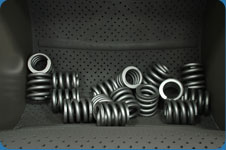
SHOT PEENING OPERATION
Shot Peening is done on the springs to clean them and to increase their fatigue life.
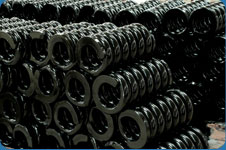
SURFACE PROTECTION
Protection against corrosion with one coat of zinc chromate primer followed by one coat of synthetic enamel is done.
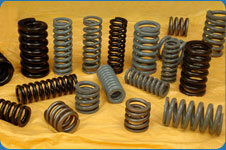
RANGE OF SPRINGS
The various type of springs which we manufacture have different bar diameter, inner diameter, outer diameter & free height. Till now the springs which are produced are for railway application and at present we are the only manufacturer in the railway sector having CNC based coiling machine.